What is Sheet Metal Design?
Full Guide About Sheet Metal Design – Sheet metal design is the process of creating three-dimensional components or parts from flat sheets of metal. This specialized design and engineering discipline entails shaping metal sheets into a variety of shapes and forms to satisfy specific functional and aesthetic needs. Because of its adaptability, strength, and cost-effectiveness, sheet metal is a popular choice for producing parts in sectors such as automotive, aerospace, construction, and electronics.
Importance of Sheet Metal Design
Effective sheet metal design is critical for achieving high-quality, efficient, and cost-effective products. It impacts factors like material usage, manufacturing processes, assembly, and even the product’s overall performance. A well-designed sheet metal part not only meets functional requirements but also minimizes waste, reduces production time, and enhances the final product’s durability.
Common Questions about Sheet Metal Design
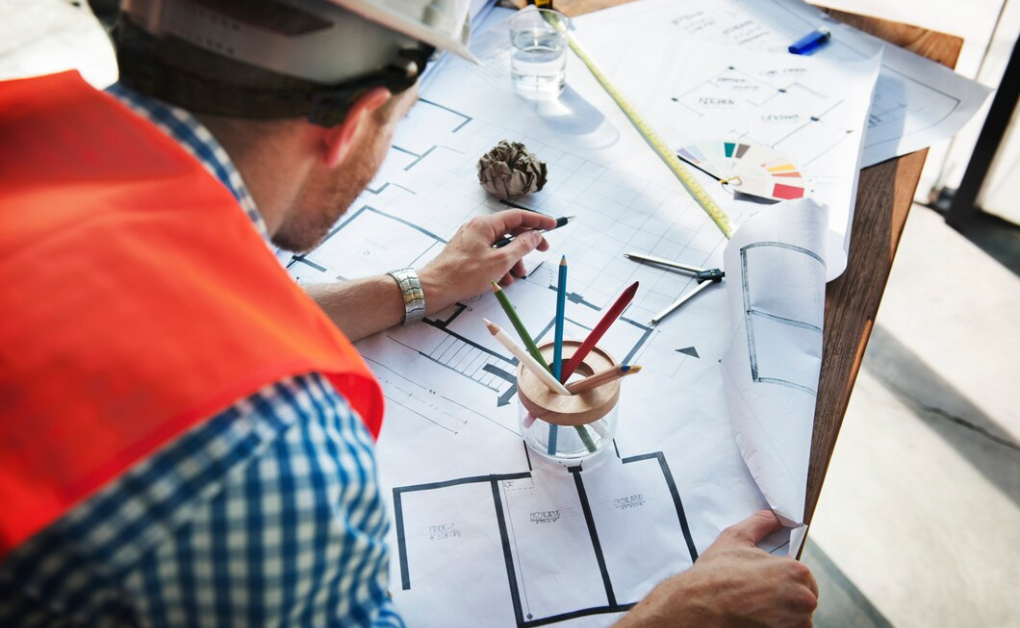
Q: Is sheet metal design compatible with modern manufacturing technologies like 3D printing and CNC machining?
A: Yes, sheet metal design can integrate with various manufacturing technologies to create complex, precise, and custom components.
Q: How does sustainability factor into sheet metal design?
A: Sustainable sheet metal design focuses on minimizing material waste, reducing energy consumption in manufacturing, and choosing eco-friendly materials and coatings.
Types of Sheet Metal Materials
In sheet metal design, you’ll encounter various types of sheet metal materials. These materials have distinct properties and applications:
- Steel: Commonly used for its strength and durability. Types include mild steel, stainless steel, and galvanized steel.
- Aluminum: Known for its lightweight properties. Varieties like the 1000 series, 5000 series, and 6000 series offer different characteristics.
- Copper: Offers excellent conductivity and corrosion resistance. Options include pure copper and copper-zinc alloys like brass.
- Titanium: Provides high strength-to-weight ratio. Choose from commercially pure titanium or titanium alloys.
- Other Alloys: Materials like nickel alloys and zinc alloys offer specialized properties for specific applications.
Selecting the right material is crucial, as it impacts the part’s strength, weight, and cost. Consider your project’s requirements and consult with experts to make an informed choice.
Factors Affecting Material Selection
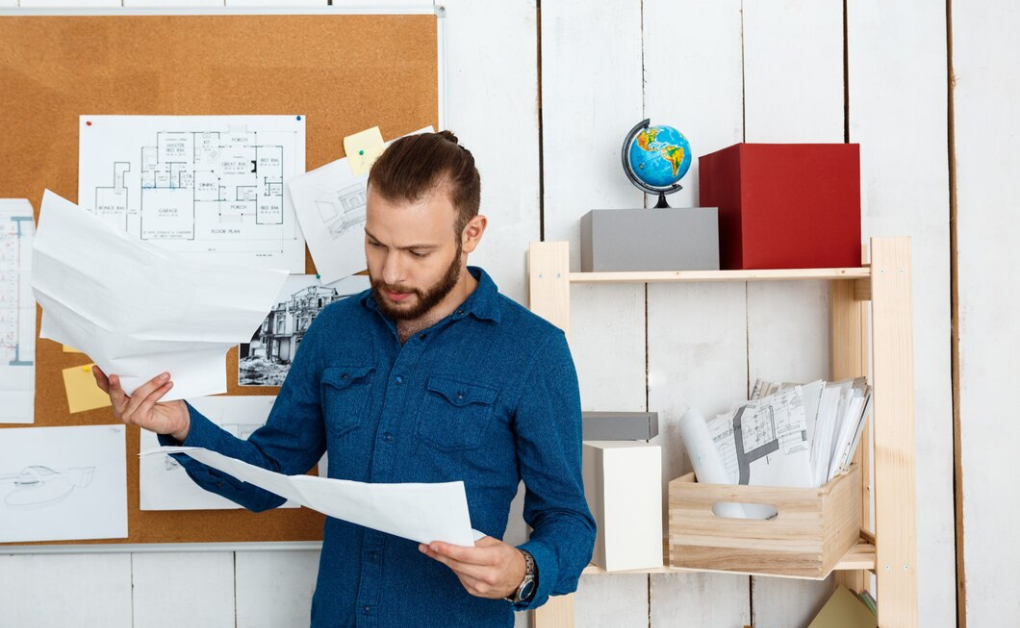
Several variables impact the selection of sheet metal material:
The choice of sheet metal material in your design is influenced by various factors:
- Strength and Durability: Consider the required strength and durability for your application. Different materials offer varying levels of strength.
- Corrosion Resistance: If your part will be exposed to corrosive environments, opt for materials with excellent corrosion resistance, like stainless steel or aluminum.
- Weight: Weight is crucial, especially in applications like aerospace or automotive. Choose materials that offer the necessary strength without adding excessive weight.
- Cost: Material cost can significantly impact your project budget. Evaluate the cost-effectiveness of your chosen material.
- Fabrication Method: The manufacturing processes you intend to use should align with the properties of your selected material. Some materials are easier to weld, cut, or form than others.
- Aesthetics: For applications where appearance matters, consider the surface finish, color, and texture of the material.
- Environmental Impact: Sustainability is increasingly important. Opt for materials that are recyclable or have a lower environmental footprint.
Balancing these factors is essential for a successful sheet metal design. Each project may prioritize different aspects, so carefully assess your specific requirements when selecting the material for your sheet metal design.
3. Design Principles
In sheet metal design, understanding key design principles is essential for creating effective and efficient components. Here are some fundamental principles:
- Bend Allowance and Deduction: These concepts address how the material stretches or compresses during bending, crucial for precise designs.
- Minimum Bend Radius: Knowing the minimum radius a material can be bent without damage ensures structural integrity.
- Flanges and Hemming: These techniques add strength and safety to your parts. Flanges provide rigidity, while hemming eliminates sharp edges.
These principles are the building blocks of successful sheet metal design. They help you create parts that are not only functional but also optimized for manufacturing and assembly. Keep them in mind as you embark on your sheet metal design journey.
4. Manufacturing Processes
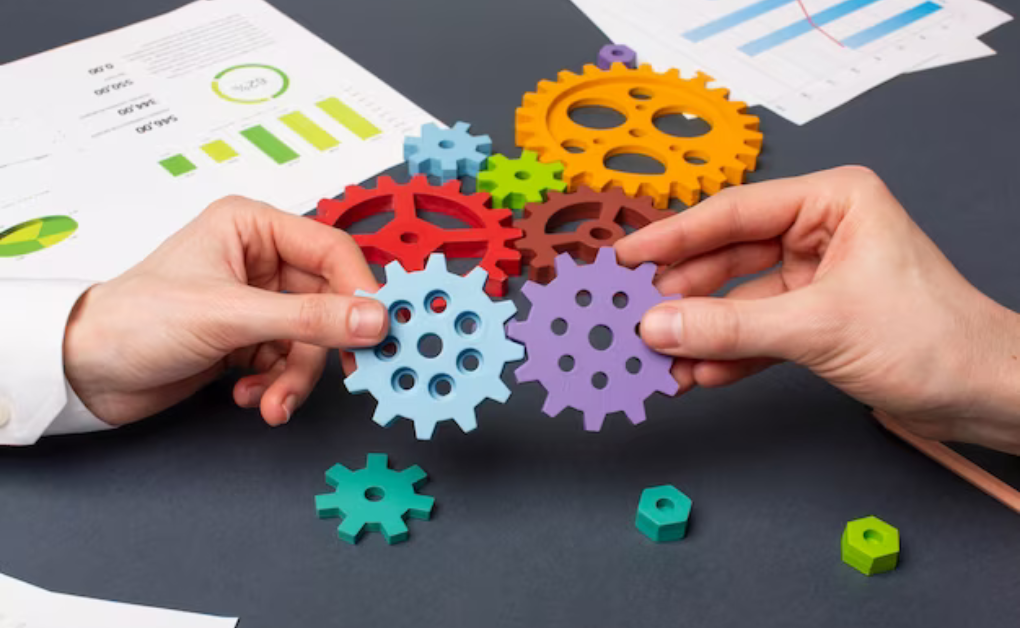
While you are learning about full guide about Sheet Metal Design, Manufacturing Processes is also an important topic . Once you’ve designed your sheet metal part, it’s essential to understand the manufacturing processes that will bring your design to life. Here’s a brief overview of key manufacturing processes in sheet metal design:
Cutting and Shearing
Laser Cutting: This method uses a high-powered laser beam to accurately cut intricate shapes in sheet metal. It’s known for precision and minimal material waste.
Waterjet Cutting: High-pressure water mixed with abrasives cuts through sheet metal, offering versatility in materials and shapes.
Shearing: Using shear blades, sheet metal is cut along straight lines, making it a cost-effective option for simple shapes.
Bending and Forming
Press Brake Bending: A press brake machine precisely bends sheet metal at specific angles, allowing for complex shapes.
Roll Forming: Sheet metal passes through rollers to achieve curved or contoured shapes, ideal for long, consistent parts.
Welding and Joining
TIG Welding (Tungsten Inert Gas): This method uses a tungsten electrode and inert gas to create high-quality welds in sheet metal.
MIG Welding (Metal Inert Gas): MIG welding employs a wire electrode and shielding gas for joining metals, suitable for various applications.
These processes are the backbone of turning your sheet metal design into a physical reality. Choosing the right process depends on your design’s complexity, material, and desired end result. Keep these options in mind as you move from design to manufacturing.
5. Design Guidelines
In sheet metal design, adhering to key guidelines ensures your projects are efficient and cost-effective:
- Optimize Material Usage: Select the right sheet metal material and thickness based on strength, weight, and cost considerations.
- Hole Placement and Tolerances: Carefully design hole sizes, shapes, and tolerances to ensure proper fit and alignment of fasteners and components.
- Tab and Slot Design: Utilize tabs and slots for easier assembly and alignment of sheet metal parts.
- Bend Radii: Adhere to minimum bend radii guidelines to prevent material damage during bending.
- Avoid Sharp Edges: Eliminate sharp edges that can pose safety hazards during handling and assembly.
- Design for Manufacturability: Collaborate with manufacturers to ensure your design is feasible for the chosen manufacturing processes.
- Minimize Welding: Reduce the need for welding whenever possible, as it can add complexity and cost.
- Consider Finish: Decide on surface finishes or coatings for aesthetics and corrosion resistance.
- Sustainability: Keep environmental impact in mind by minimizing material waste and considering recyclable materials.
- Quality Control: Implement quality control measures, including inspection and testing, to ensure the final product meets design specifications.
By following these design guidelines, you can create sheet metal components that are not only functional but also efficient to produce and assemble.
6. Tolerances and Quality Control
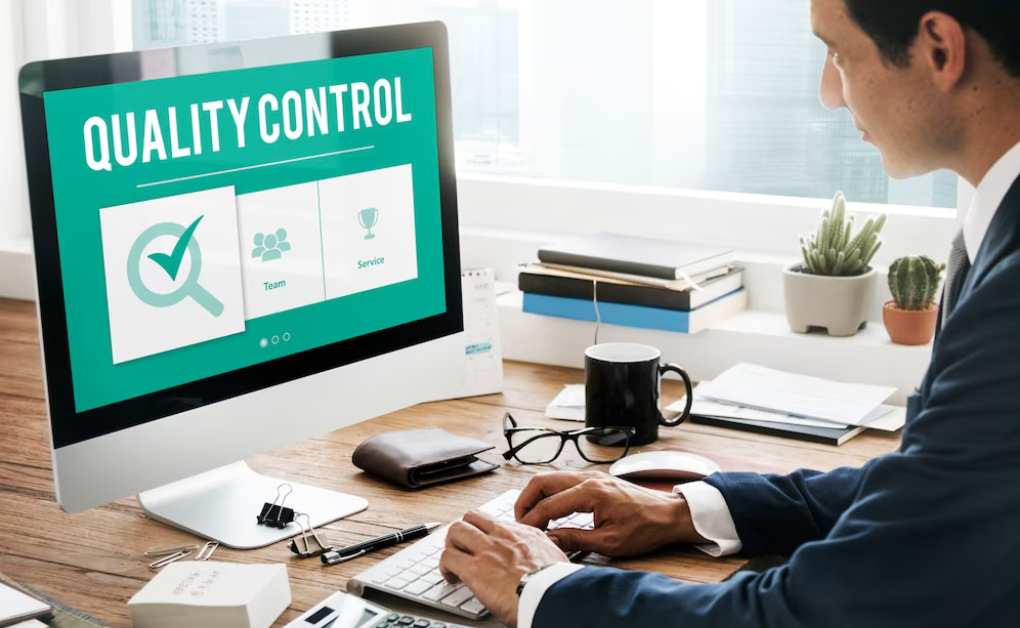
In sheet metal design, precision is paramount. Tolerances refer to allowable variations in dimensions, ensuring that your sheet metal parts meet design specifications. Here’s a concise overview:
1. Tolerance Basics: Tolerances are specified in drawings using symbols and values. They control factors like size, form, and orientation.
2. Importance of GD&T: Geometric Dimensioning and Tolerancing (GD&T) is a standardized system that helps define and communicate tolerances clearly.
3. Inspection Methods: To maintain quality, employ visual checks, coordinate measuring machines (CMMs), or non-destructive testing (NDT) techniques like X-ray inspection or ultrasonic testing.
4. Common Quality Issues: Be vigilant for problems such as warping, distortion, surface imperfections, and dimensional inaccuracies, which can impact your sheet metal parts.
5. Collaboration: Work closely with your manufacturing partners to ensure that tolerances are met, and quality is maintained throughout production.
By understanding tolerances and implementing rigorous quality control measures, you’ll ensure that your sheet metal designs meet the highest standards for accuracy and reliability.
Quick Prototyping
Prototyping is an important phase in sheet metal design since it allows you to test and refine your ideas before moving on with mass production. Rapid prototyping processes, such as 3D printing and CNC machining, can aid in the production of prototypes in a timely manner.
Physical Testing
Physical testing involves subjecting sheet metal parts to various conditions, such as stress, load, and environmental factors, to evaluate their performance and durability.
Q: What advantages does fast prototyping provide in sheet metal design?
A: Rapid prototyping enables rapid iteration, low-cost testing, and the detection of design defects prior to mass manufacturing.
Hope this, Full Guide About Sheet Metal Design will help you understand better about sheet metal design.